Development of Ultra-High Molecular Weight Polyethylene Coating
Large Potential for Improvement of Environmental Resistance Capacity and Surface Functionalization of Industrial Structural Materials
2008.03.13
National Institute for Materials Science
A team led by Senior Researcher Jin Kawakita of the Composites and Coatings Center of the National Institute for Materials Science developed a spray method which enables high speed coating without deterioration of material properties in the atmosphere by proper heating and acceleration of a powder of ultra-high molecular weight polyethylene.
Abstract
- A team led by Senior Researcher Jin Kawakita of the Composites and Coatings Center of the National Institute for Materials Science (President: Teruo Kishi) developed a spray method which enables high speed coating without deterioration of material properties in the atmosphere by proper heating and acceleration of a powder of ultra-high molecular weight polyethylene.
- Because ultra-high molecular weight polyethylene has poor fluidity, coating methods in which the powder is melted and fluidized cannot be used. Among other methods, coating by dispersion in organic solvents has a serious environmental impact, and with thermal spray techniques, thermal deterioration of the material during film forming is unavoidable.
- Therefore, starting from a review of heating methods suited to the thermal properties of plastic materials in atmospheric thermal spray processes, a spray method (warm spray) enabling coating while suppressing thermal deterioration of the material, which was established by this group, was employed in order to use plastic materials with low thermal conductivity and decomposition temperatures in comparison with metals and inorganic oxides. The developed technology was then realized by adopting a spray gun structure which makes it possible to heat/accelerate the material over an extended time at a lower temperature than with the conventional technique.
- With the ultra-high molecular weight polyethylene coating obtained by this method, thermal deterioration in the production process is reduced, and prevention of water permeation with a film thickness of 50 microns was confirmed. Based on these results, it is considered possible to apply this coating to resin covers for various kinds of rolls used in printing presses, and to environment-resistant coatings for use in chemical plants and marine structures. The developed spray method also has high potential for application to a wide range of other thermoplastic materials. Thin film forming of high performance engineering plastics such as PEEK is also expected.
- The results of this research are scheduled to be announced at the International Thermal Spray Conference to be held in June 2008 in Netherland.
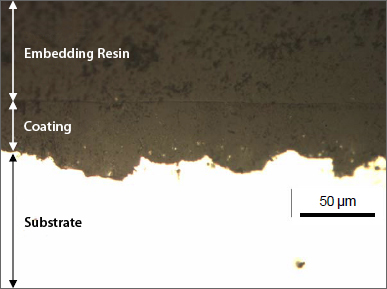
Fig. : Embedded resin for cross-sectional observation