Success in Development of Manufacturing Technology of Cast and Wrought Alloys with the World’s Highest Temperature Capability for Aircraft Engines
2009.03.13
Mitsubishi Materials Corporation
National Institute for Materials Science
Mitsubishi Materials Corporation and the National Institute for Materials Science, have succeeded in the development of a manufacturing technology of cast and wrought alloys with the world’s highest temperature capability and in the production of turbine disk pancakes with the processing equipments in Japan for aircraft engines.
Abstract
- Mitsubishi Materials Corporation (President: Akihiko Ide, hereinafter, Mitsubishi Materials) and the National Institute for Materials Science (President: Prof. Teruo Kishi, hereinafter, NIMS), have succeeded in the development of a manufacturing technology of cast and wrought alloys with the world’s highest temperature capability and in the production of turbine disk pancakes with the processing equipments in Japan for aircraft engines.
- This research and development effort was made over a 2-year period from 2007FY to 2008FY under a commission from the New Energy and Industrial Technology Development Organization (NEDO). Aiming at practical application of products using nickel-cobalt-based high temperature alloys (TMW alloys) developed by NIMS, the development of the manufacturing technology was carried out at Mitsubishi Materials’ Okegawa Plant. The newly-developed process includes melting of ton-class ingots, forging processes, and heat treatment.
- Conventionally, nickel-based wrought superalloys, which provide excellent heat resisting properties, have been used for the parts serviced in high temperature and high stress such as aircraft engine turbine disks and compressor blades. In order to increase the temperature capability of high temperature alloys used for turbine disks, normally it is needed to add various refractory elements, which results in the problems of deviations in chemical composition and susceptibility to cracking in the manufacturing (i.e., forging) process. To overcome these problems, NIMS developed nickel-cobalt-based TMW alloys with both high temperature strength and good forgeability. In this NEDO project, prototype turbine pancakes of TMW alloys with a size enabling practical application (φ440mm), and a homogeneous microstructure of a 10μm grain size was successfully produced by selecting appropriate ingot melting conditions. The high temperature properties of the turbine disk material were evaluated in a creep test (Note 1), confirming that it has the world’s highest temperature capability for forgeable products which is more than 50°C higher than that of the strongest commercial cast and wrought superalloy, Undimet 720Li.
- As the key aircraft engine component, turbine disk is a large-scale part that rotates under a particularly high temperature and high pressure environment, therefore, extremely high reliability is required. Until now, the disks used in all aircraft engines in Japan and other countries have been developed in the United States or Europe. In recent years, on the viewpoint of reducing fuel consumption in flight, higher service temperatures have been required for materials, which allow aircraft engines to operate at higher temperatures than in the past. With the establishment of the practical manufacturing process in actual application scale and demonstration of the high temperature properties, Japanese-produced turbine blades and disks using NIMS-developed alloys can be expected to enter into the domestic and foreign markets for aircraft engines and industrial gas turbines in the near future.
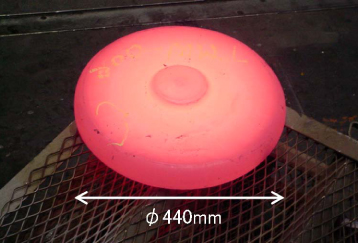
Turbine disk pancake of press-forged TMW alloy