Dramatic Improvement in Hardness and Smoothness of Superhard Coating
Technical Innovation in Wear-resistant Coating for Industrial Use
2009.11.30
National Institute for Materials Science
Fujimi Incorporated
The Hybrid Materials Center of the National Institute for Materials Science, in joint work with Fujimi Incorporated, succeeded in fabricating a WC-Co coating for wear resistance applications.
Abstract
- The Hybrid Materials Center of the National Institute for Materials Science (NIMS; President: Sukekatsu Ushioda), in joint work with Fujimi Incorporated (President: Keishi Seki), succeeded in fabricating a WC-Co coating for wear resistance applications. The new coating, which features dramatically improved surface smoothness and hardness in comparison with the conventional coating, was realized using a combination of a new coating process developed by NIMS and a raw material powder developed by Fujimi Incorporated.
- Sintered materials consisting of tungsten carbide (WC) and cobalt (Co) are termed cemented carbides, and are widely used as tools for machining applications, taking advantage of their outstanding hardness and toughness. Coatings which are obtained by thermal spraying using WC-Co powder as the raw material are widely used as wear-resistant coatings for the rolls used in steel and paper manufacturing plants, as well as in construction machinery and other applications. However, because cobalt is melted during thermal spraying, the formation of weak, brittle binder phase in the coating by reaction between the cobalt and tungsten carbide was a problem in the conventional thermal spraying process. Although reducing the size of the raw material powder was known to be effective for improving the properties of the coating, adhesion of molten particles inside the thermal spraying nozzle caused a phenomenon called “spitting,” which made it impossible to continue operation for long hours. This was a technical barrier to stable application of such coatings to large components.
- NIMS developed a “Warm Spray” process, in which the temperature of the gas used in thermal spraying is controlled by mixing an appropriate amount of nitrogen in the combustion flame. In the present work, this process was applied to the newly-developed WC-Co powder. As a result, it was possible to perform thermal spraying with the powder accelerated to a high velocity exceeding 500m/s while also suppressing fusion of the cobalt in the raw material powder, suggesting the prospect of solving the above-mentioned problem.
- Fujimi Incorporated developed a granule-shaped powder (granule particle size: 5-20 μm) using nano- to submicron-size WC particles optimized for the Warm Spray process. In principle, fine WC particles are effective for improving the hardness of the coating, while small granules are effective in reducing surface roughness. However, with the conventional thermal spraying process, the formation of weak compounds and increased frequency of spitting were problems when fine materials were used. In this project, the formation of the weak binder phase was suppressed mostly and a stable coating operation was achieved by using the new material in combination with the NIMS Warm Spray process.
- The developed coating film displayed a Vickers hardness exceeding Hv1600 and surface roughness of Ra1.6 μm or less without post-spray treatment, and thus achieved a dramatic improvement in properties in comparison with the conventional coating. Because the new coating is expected to provide excellent wear resistance due to its high hardness, and also greatly reduces surface finishing time after spraying, considerable cost reduction can be expected in manufacturing and use.
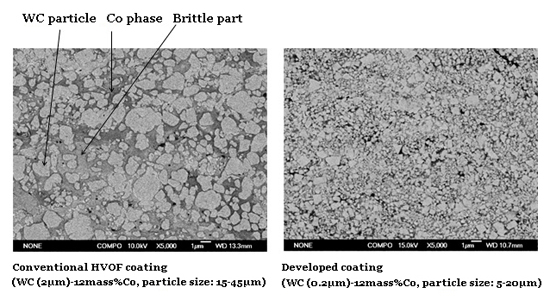
Fig:Images of microstructures of conventional and developed coating films.(The white part between WC particles in the conventional coating is brittle.)
Related File / Link