Treating Pulmonary Diseases Using Alaska Pollock Gelatin
Development of Strong Sealant That Remains Liquid at Room Temperature and Helps Shorten Surgical Operations
2015.10.15
(2015.10.23 Update)
National Institute for Materials Science (NIMS)
Researchers at NIMS developed a new sealant to close holes developed in lungs and blood vessels using Alaska pollock gelatin.
Abstract
Furthermore, the researchers explain that the advantage of the sealant is its property of remaining liquid at room temperature as it contains gelatin extracted from Alaska pollock, which is a cold-water fish. “The sealant doesn’t have to be preheated before surgery, and it can be sprayed directly on an open wound after mixing it with a crosslinking agent. Because it possesses extremely high bonding strength and elasticity, and it slowly breaks down in the body after surgery, it has the potential to be used as a sealant for any organ.”
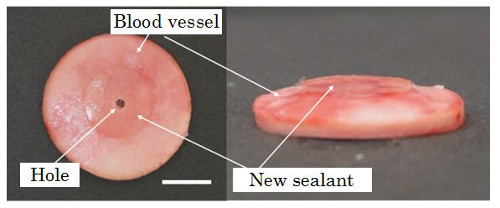
Figure 1: The newly developed sealant that was applied over a 3-mm-diameter hole in a porcine blood vessel.
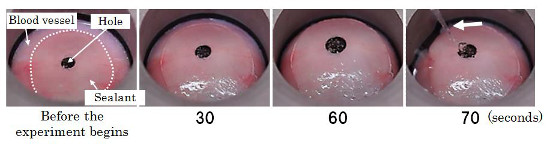
Figure 2: Observation of sealant applied over a hole that was created in a porcine blood vessel. After the application, saline was used to make the tissue swell. In this experiment, the commercially-available sealant applied burst only in a few seconds; in contrast, the sealant we developed maintained its integrity for 70 seconds (the arrow is pointing at saline vigorously coming out of the burst sealant). These results indicate that the new sealant was significantly stronger than the commercially-available sealant in terms of interfacial strength between the sealant and blood vessel.