Development of Warm Multidirectional Compact Rolling Process Enabling Continuous Production of High Strength/High Formability Super Steel Wire
Success in Trial Mass Production of 100,000 Super Steel Micro Screws.
Potential for Large Reduction in CO2 Emissions during Part Manufacturing
2008.05.21
National Institute for Materials Science
A team led by Dr. Shiro Torizuka, Group Leader, Materials Reliability Center, National Institute for Materials Science developed a warm multidirectional compact rolling process which enables continuous production of super steel wire that possesses both high strength and high formability.
Abstract
- A team led by Dr. Shiro Torizuka, Group Leader, Materials Reliability Center, National Institute for Materials Science (President: Teruo Kishi) developed a warm multidirectional compact rolling process which enables continuous production of super steel wire that possesses both high strength and high formability. Using this super steel wire as material, the micro-fastener manufacturer Furiya Giken Co., Ltd. (President: Yoshiyuki Suzuki) successfully trial manufactured M1.7 micro screws for use in cellphones at the mass production level (105 pieces), demonstrating the industrial potential of this compact process and the super steel wire. This achievement is the world’s first successful mass production of submicron ultra-fine grained steel at the actual machine level.
- Formation of a fine grained microstructure can be realize by forming under large strain in the warm temperature region (around 500°C). Various large strain forming methods have been proposed, including the ECAP (Equal Channel Angular Processing) method, ARB (Accumulative Roll Bonding) method, HPT (High Pressure Torsion) method, and others, and excellent results have been reported in basic research. However, no production method for ultra-fine grained steel had been established as an industrial technology. Because the viewpoint of continuous production had been lacking in conventional research on fine grained steel, laboratory level results had not led to practical application.
- It is possible to form ultra-fine grains efficiently by heavy deformation of steel from multiple directions, that is, from the vertical and horizontal directions. Although heavy deformation from these two directions is possible in forging, it was difficult in rolling processes. In this work, a compact rolling mill which is capable of continuously realizing horizontal-vertical rolling, i.e., multidirectional rolling was developed. By locating a high frequency heating device in close proximity to the rolling mill, the NIMS team also succeeded in developing a warm rolling system that enables multidirectional rolling while continuously heating the wire rod material, thereby realizing a compact process for continuous production of super steel wire. As material for rolling by the developed process, satisfactory results can be obtained using hot rolled coils with a diameter of 5.5-6.0mm, which are available in large quantity in the commercial market. Because addition of special elements is not necessary, economical production can be expected.
- Super steel wire can be produced in the range of diameters from 0.2mm to 3mm. Because its strength exceeds 1GPa4) and its drawing value is 65% or more, it has an extremely high strength-drawing balance. In trial manufacturing of 100,000 M1.7 micro screws using 20kg of this super steel wire, there was absolutely no breakage of the screw head, as frequently occurs with other high strength materials, demonstrating that this material possesses excellent formability. These super steel screws have strength on the same level as conventional screws manufactured by the quenching and tempering process. Furthermore, because spheroidizing of carbides can be realized simultaneously with grain refinement, it is possible to omit the conventional spheroidizing annealing in the wire rod material production process. This compact process makes it possible to omit processes that have a large environmental impact, namely, spheroidizing annealing and quenching and tempering, which had been essential when manufacturing wire and high strength parts, and thus has the potential to substantially reduce the CO2 emissions in part manufacturing.
- The compact process developed in this research can be used not only in the production of wire, but also in the production of thin band products (thickness: 0.2mm). As parts, a wide range of applications can be expected, not limited to screws, but also including shafts, pins, and other products.
- A portion of these research results is scheduled for presentation the Conference of the Japan Society for Technology of Plasticity to be held May 24-25, 2008.
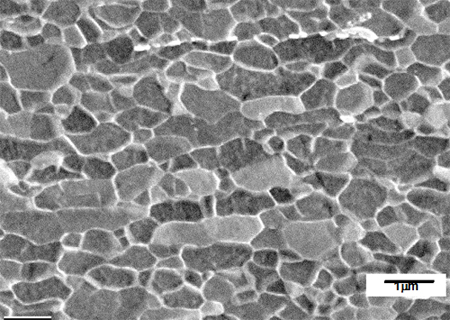
Figure: Micro organization of super-steel wire(average particle size 0.5 microns)