高強度・高成形性超鉄鋼ワイヤーの連続生産を可能にする
温間多方向コンパクト圧延プロセスの開発
超鉄鋼マイクロネジ10万個量産化試作に成功。
部品製造時の二酸化炭素ガス排出量大幅削減の可能性
2008.05.21
独立行政法人物質・材料研究機構
NIMS量子ドットセンターは東北大学 多元物質科学研究所と共同で、微小球共振器を自己組織化的に並べることで、直角曲げが可能なミクロンスケールの光配線と分波器の開発に成功した。
概要
- 独立行政法人物質・材料研究機構 (理事長 : 岸 輝雄) 材料信頼性センター 鳥塚 史郎グループリーダーらは、高強度でかつ高成形性の超鉄鋼ワイヤーの連続生産を可能にする温間多方向コンパクト圧延プロセスを開発した。本超鉄鋼ワイヤーを素材として、 (株) 降矢技研 (社長 : 鈴木 由幸) にて、M1.7携帯電話用マイクロネジの試作を行ったところ、10万個の量産化レベル試作に成功し、本コンパクトプロセスおよび超鉄鋼ワイヤーの工業的な有効性を実証した。サブミクロン超微細粒鋼を実機レベルの量産化に成功した世界初の成果である。
- 微細粒組織の生成は、温間温度域 (500℃付近) での大ひずみ加工によって実現できる。ECAP法 (Equal channel angular pressing) 、ARB法 (繰り返し重ね圧延) 、HPT法(High pressure torsion)など大ひずみ加工方法が提案され、優れた基礎研究結果が報告されてきたが、生産技術としての超微細粒鋼の製造方法は未確立であった。従来の微細粒研究においては、連続化という視点が欠けており、ラボレベルの成果が実用化に結びついていなかった。
- 鉄を、多方向から、すなわち、縦横から大きく潰すことによって、効率的に超微細粒の生成が可能である。縦横から大きく潰すことは、鍛造では可能であるが、圧延では難しかった。今回、この縦横圧延、すなわち、多方向圧延を連続的に実現でき、かつ、コンパクトな圧延機を開発した。さらに、圧延機のすぐそばに高周波加熱装置を配置することにより、線材が連続的に加熱されながら、多方向圧延される温間圧延システムの開発にも成功し、超鉄鋼ワイヤーの連続生産用コンパクトプロセスを実現できた。素材は、市場に大量に供給されている直径5.5-6.0mmの熱延コイルを用いればよく、特別な成分の添加は必要ないため、安価な製造が期待できる。
- 超鉄鋼ワイヤーは直径0.2-3mmの範囲で製造可能であり、強度は1GPaを越え、絞り値は65%以上あるため、きわめて強度 - 絞りバランスが高い。本超鉄鋼ワイヤー20kgを用いて、M1.7マイクロネジ10万個の試作をおこなったところ、高強度材でしばしば発生するねじ頭部の割れは一切無く、成形性がよいことが実証された。本超鉄鋼ネジは焼入・焼戻しで製造される従来ネジと同等の強度を有した。また、超微細粒化は炭化物の球状化も同時に実現できるため、線材製造時の球状化焼鈍も省略可能である。本コンパクトプロセスによって、ワイヤーおよび高強度部品製造時に必須であった球状化焼鈍や焼入・焼戻しといった環境負荷が大きい工程を省略できるため、部品製造時の二酸化炭素ガス排出量大幅削減の可能性を示すものである。
今回開発したコンパクトプロセスはワイヤーだけではなく、薄帯板 (厚さ0.2mm) の製造も可能である。部品としてはネジだけではなくシャフト、ピンなどへの幅広い応用が期待できる。 - 今回の研究成果の一部は2008年5月24~25日の日本塑性加工学会で発表を予定している。
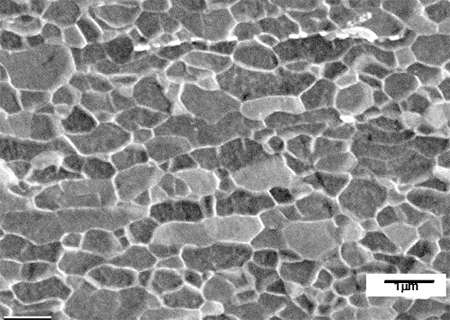
プレス資料中の図3: 超鉄鋼ワイヤーのミクロ組織 (平均粒径0.5ミクロン)